Post-processing transforms raw 3D printing outputs into refined, functional components. You rely on it to improve surface quality, mechanical strength, and dimensional accuracy. It optimizes production workflows, enabling scalability and better product usability. Automation and innovation revolutionize these processes, reducing manual labor and ensuring consistent results. Investing in advanced post-processing technology elevates your manufacturing capabilities.
Key Takeaways
- Post-processing is important to improve 3D-printed parts. It fixes rough surfaces and weak strength, making products better for use.
- Using machines for post-processing, like cleaning powder or polishing, saves time and makes work consistent. These tools can lower costs and speed up production.
- Matching post-processing methods to the type of 3D printing is key. For example, cleaning powder works for powder prints, and curing helps resin prints. This improves results and product quality.
Overview of Post-Processing in 3D Printing
Necessity of Post-Processing
Post-processing is essential for transforming raw 3D-printed parts into functional and visually appealing products. Without it, you may encounter rough surfaces, weak mechanical properties, or dimensional inaccuracies. These issues can compromise the usability and durability of your components. Post-processing ensures that your parts meet industry standards and customer expectations.
The growing adoption of 3D printing highlights the importance of post-processing. For instance:
- Production volumes are increasing, with 76% of manufacturers printing more than 10 parts in 2023.
- The percentage of those producing over 1,000 parts rose from 4.7% to 6.2%, reflecting a shift toward end-use production.
- 82% of companies report significant cost savings due to 3D printing, emphasizing the need for efficient post-processing to maintain these benefits.
Challenges in Post-Processing
Post-processing presents several challenges, especially when dealing with intricate designs or large production volumes. Depowdering, for example, can be particularly complex. Powder often gets trapped in detailed geometries, making manual cleaning inefficient. This inefficiency becomes more pronounced when scaling up production.
Automation is addressing these challenges. Systems like the SFM-AT800S use controlled vibrations and motorized rotation to streamline depowdering. However, adopting such technologies requires investment and training, which can be barriers for smaller operations.
Post-Processing Needs for Different 3D Printing Technologies
Different 3D printing technologies demand unique post-processing approaches. For instance, powder-based methods often require depowdering, while resin-based techniques involve curing and support removal. Post-processing times vary significantly, sometimes taking one hour for every one to six hours of printing.
Labor and space requirements also differ. You might need one to three finishers for every machine operator, and facilities often allocate half to one square foot of post-processing space for every square foot of printer space. These factors highlight the need for tailored workflows to optimize efficiency and scalability.
Key Technologies and Methods in Post-Processing
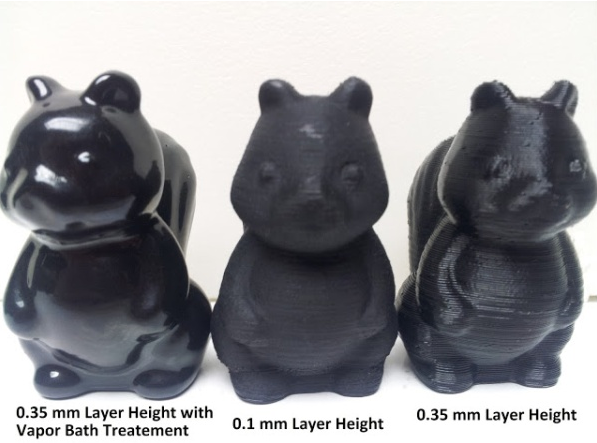
Depowdering for Powder-Based 3D Printing
Depowdering plays a vital role in post-processing for powder-based 3D printing. It ensures that excess powder is removed from both the exterior and interior surfaces of printed parts. This step is critical for improving mechanical properties and achieving a smooth surface finish. Traditional manual methods often fall short, especially when dealing with intricate geometries. They can damage precision structures and fail to clean hard-to-reach areas effectively.
Automated depowdering systems, such as BLT machines, address these challenges. These systems use advanced techniques like flipping, rotating, and vibrating to ensure thorough cleaning. They can handle large and complex parts while maintaining structural integrity. Additionally, safety features like CE and ATEX certifications and sealed glove boxes minimize risks associated with powder handling. By adopting automated depowdering, you can enhance product quality and improve powder recycling efficiency, making your workflow more sustainable and reliable.
Tip: Investing in automated depowdering systems not only saves time but also reduces the risk of human error, especially for high-volume production.
Surface Finishing Techniques
Surface finishing transforms rough, raw prints into polished, professional-grade components. Techniques like sanding, tumbling, and chemical smoothing are commonly used to achieve the desired texture and appearance. Sanding works well for small-scale projects, while tumbling is ideal for batch processing. Chemical smoothing, on the other hand, uses solvents to create a glossy finish, particularly for materials like ABS.
You should choose a surface finishing method based on the material and application of your 3D-printed part. For example, medical devices often require a smooth, sterilizable surface, while consumer goods may prioritize aesthetics. By selecting the right technique, you can enhance both the functionality and visual appeal of your products.
Heat Treatments and Annealing
Heat treatments, including annealing and normalizing, improve the mechanical properties of 3D-printed parts. These processes relieve internal stresses, enhance ductility, and increase strength. Annealing softens the material and refines its grain structure, while normalizing boosts toughness and impact resistance.
Process |
Purpose |
Resulting Properties |
---|---|---|
Annealing |
Relieves stress, increases ductility |
Softer, improved grain structure |
Normalizing |
Enhances strength and toughness |
Stronger, tougher, better impact resistance |
By incorporating heat treatments into your post-processing workflow, you can ensure that your parts meet the mechanical demands of their intended applications. This step is particularly important for industries like aerospace and automotive, where material performance is critical.
Support Removal for Complex Designs
Support structures are essential for printing overhangs and intricate geometries, but they must be removed carefully to avoid damaging the final part. Manual removal can be time-consuming and may leave marks or imperfections. Automated solutions streamline this process, ensuring precision and efficiency.
For example, the Institute of Architecture at Hochschule Mainz successfully used SLA technology to create detailed models of medieval German cities. They managed support removal effectively, producing six large-scale models that showcased city development over 450 years. Similarly, RPBW utilized 3D printing for architectural models, accelerating the design process by efficiently handling support structures. These examples highlight the importance of adopting advanced support removal techniques for complex designs.
Coloring and Aesthetic Enhancements
Coloring and aesthetic enhancements elevate the visual appeal of 3D-printed parts. Techniques like painting, dyeing, and electroplating allow you to customize the appearance of your products. Painting offers versatility, enabling you to match specific color schemes or branding requirements. Dyeing works well for porous materials like nylon, while electroplating adds a metallic finish for a premium look.
These enhancements are particularly valuable for consumer goods and decorative items. By investing in aesthetic post-processing, you can create products that stand out in competitive markets. Additionally, advanced coloring techniques can improve UV resistance and durability, extending the lifespan of your parts.
Innovations in Automation for Post-Processing
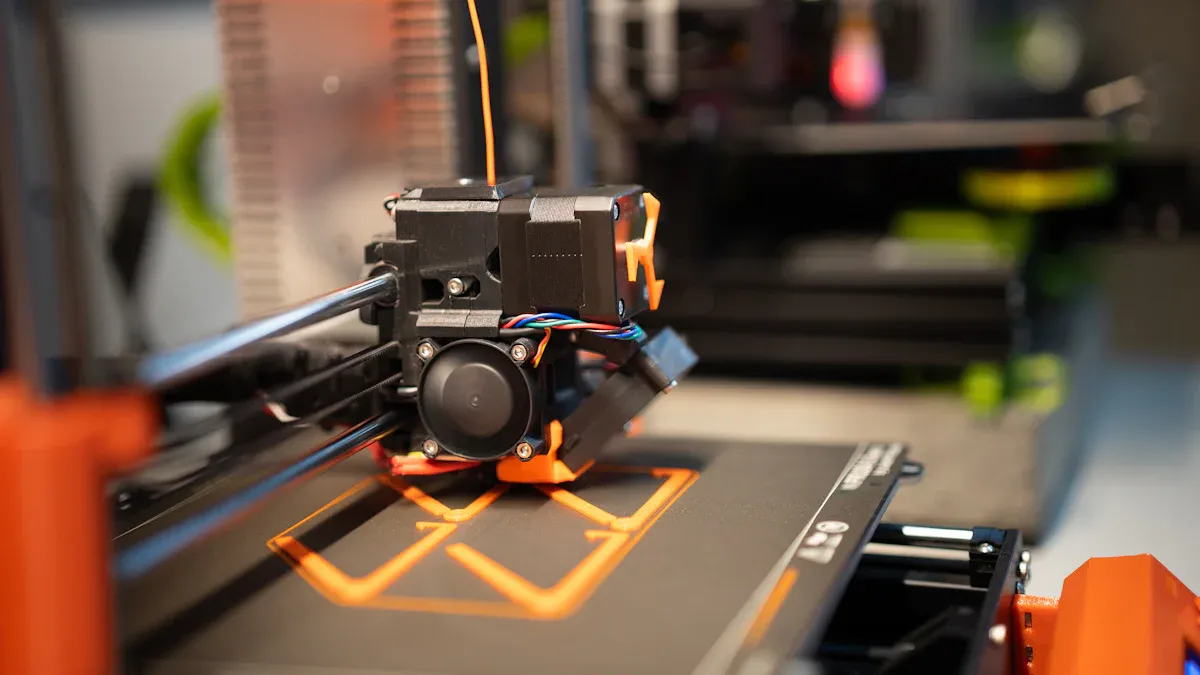
Automated Depowdering Systems
Automated depowdering systems have revolutionized post-processing for powder-based 3D printing. These systems eliminate the inefficiencies of manual cleaning, which often consumes significant time and risks damaging intricate parts. For example, the DyeMansion Powershot C offers a reliable alternative to manual methods. It reduces production costs while maintaining high-quality standards, making it an essential tool for scaling up operations.
By automating depowdering, you can achieve consistent results across batches and improve powder recycling efficiency. This not only enhances sustainability but also minimizes labor-intensive tasks. Advanced systems use techniques like controlled vibrations and motorized rotations to clean even the most complex geometries. These innovations ensure that your parts meet the highest quality standards without compromising structural integrity.
Note: Investing in automated depowdering systems can significantly reduce production time and costs, especially for high-volume manufacturing.
Robotic Surface Finishing
Robotic surface finishing systems bring precision and efficiency to post-processing workflows. These systems use advanced robotics to polish, sand, or smooth surfaces with unparalleled accuracy. In industries like aerospace, robotic polishing enhances surface quality while reducing processing time. Precise control over pressure ensures consistent results, minimizing manual errors and improving overall product reliability.
In the automotive sector, robotic sanding has demonstrated significant efficiency gains. It reduces manual labor costs and accelerates production timelines. Additionally, robotic systems adapt to material variations, ensuring a uniform finish across all parts. By incorporating robotic surface finishing into your workflow, you can achieve superior quality while optimizing resource allocation.
Key Benefits of Robotic Surface Finishing:
- Enhanced surface quality through precise control.
- Reduced processing time and labor costs.
- Consistent results across batches, regardless of material differences.
AI-Driven Quality Control
AI-driven quality control systems are transforming how you ensure product integrity in 3D printing post-processing. These systems use advanced algorithms to detect defects, monitor processes, and optimize workflows. Immediate defect detection reduces the time spent on unsuccessful prints, improving production efficiency.
Quality control metrics highlight the effectiveness of AI-driven systems:
Metric |
Description |
---|---|
Cost Savings |
Reduces labor costs by minimizing manual inspections and allows for prompt intervention to avoid costly reprints. |
Material Savings |
Mitigates waste by stopping prints upon defect detection, leading to more sustainable material use. |
Time Savings |
Enables immediate defect detection, reducing time spent on unsuccessful prints and improving production efficiency. |
AI systems also enhance material quality and process control. They perform non-destructive testing and post-processing inspections, ensuring compliance with industry standards. By adopting AI-driven quality control, you can deliver products that meet customer expectations while reducing operational costs.
Workflow Integration for Efficiency
Integrating automated workflows into your post-processing operations streamlines the entire production cycle. Automation reduces manual tasks, allowing your team to focus on critical efforts. For instance, healthcare facilities using automated revenue cycle solutions have reported a 25% reduction in claim denials and a 15% increase in on-time payments.
In 3D printing, automation improves speed and scalability. It addresses common challenges like time consumption and inconsistency in post-processing. Studies show that post-processing can add 17% to 100% to the total production time. Automation mitigates these delays, ensuring faster turnaround times and consistent results.
Advantages of Workflow Integration:
- Decreased operational costs through better resource allocation.
- Enhanced scalability for high-volume production.
- Improved product quality and reduced lead times.
By integrating automated workflows, you can optimize efficiency and maintain a competitive edge in the rapidly evolving 3D printing industry.
Case Studies and Real-World Applications
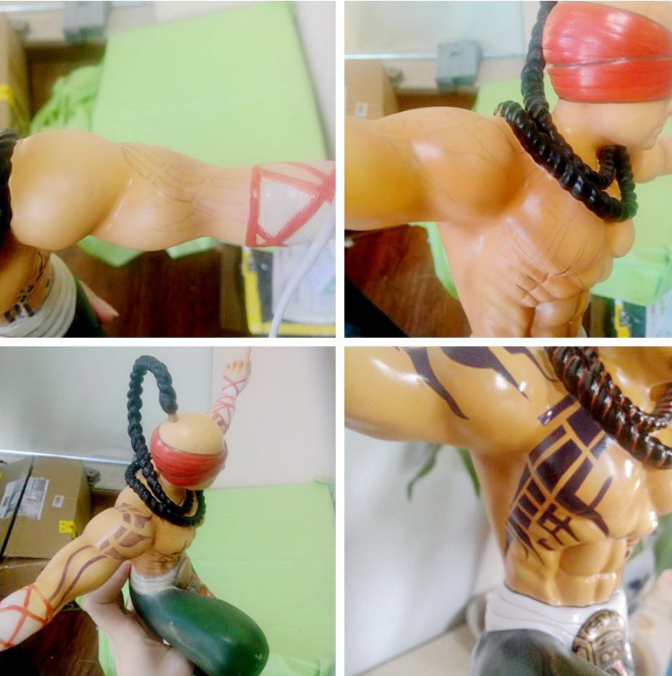
Aerospace and Automotive Applications
In aerospace and automotive industries, post-processing ensures that 3D-printed components meet stringent performance and safety standards. You rely on heat treatments to enhance material strength and durability, making parts suitable for high-stress environments. For example, turbine blades and engine components undergo annealing to withstand extreme temperatures and pressures.
Surface finishing also plays a critical role. Polished surfaces reduce drag and improve aerodynamic efficiency in aerospace applications. In automotive manufacturing, robotic sanding ensures a flawless finish for exterior parts, enhancing both aesthetics and functionality. By integrating advanced post-processing techniques, you can achieve superior quality and reliability in these demanding sectors.
Medical Industry: Precision and Sterility
The medical field demands precision and sterility in every component. Post-processing ensures that 3D-printed implants, surgical tools, and prosthetics meet these requirements. You can use chemical smoothing to create surfaces that are easy to sterilize, reducing the risk of infection.
Heat treatments further enhance the mechanical properties of medical devices, ensuring they perform reliably under stress. For instance, orthopedic implants benefit from annealing, which improves their strength and biocompatibility. By adopting tailored post-processing workflows, you can produce medical-grade components that meet strict regulatory standards.
Consumer Goods: Aesthetic and Functional Improvements
Post-processing transforms 3D-printed consumer goods into visually appealing and functional products. Techniques like painting, dyeing, and electroplating allow you to customize colors and finishes, aligning with market trends and branding needs. Studies show that consumers associate imperfections in processed goods with higher levels of care and craftsmanship. By leveraging this perception, you can enhance the appeal of your products.
For example, dyeing porous materials like nylon creates vibrant, long-lasting colors, while electroplating adds a premium metallic finish. These enhancements not only improve aesthetics but also extend product lifespan. By investing in advanced post-processing, you can create consumer goods that stand out in competitive markets.
Benefits and Future Trends in Post-Processing
Enhancing Efficiency and Reducing Lead Times
Post-processing advancements significantly improve efficiency and reduce lead times. By automating repetitive tasks, you can eliminate human errors and streamline workflows. Shorter lead times allow you to respond quickly to market demands, enhancing agility and customer satisfaction.
Key benefits of reducing lead times:
- Streamlined workflows improve operational efficiency.
- Faster product delivery enhances customer satisfaction.
- Optimized processes provide a competitive edge.
Automation tools, such as machine data platforms, further enhance efficiency by reducing unnecessary steps. Improved communication and collaboration between teams also play a vital role in minimizing delays. These strategies ensure that your production cycle remains fast and reliable.
Scalability for Mass Production
Post-processing innovations enable you to scale 3D printing operations for mass production. Automated systems handle large volumes of parts with consistent quality, reducing the need for manual intervention. This scalability is crucial for industries like automotive and consumer goods, where high production rates are essential.
By integrating automated workflows, you can allocate resources more effectively and maintain consistent output. This approach not only reduces costs but also ensures that your products meet industry standards, even at scale. As demand for 3D-printed components grows, scalable post-processing solutions will become indispensable.
Sustainability in Post-Processing
Sustainability is a growing priority in post-processing. By adopting eco-friendly practices, you can reduce waste and conserve resources. For example, automated depowdering systems improve powder recycling efficiency, minimizing material waste. Transparency in environmental reporting also drives continuous improvement in sustainability practices.
Benefit Type |
Description |
---|---|
Resource Efficiency |
Identifying high resource consumption areas can lead to cost savings through reduced resource use. |
Waste Reduction |
Strategies developed from sustainability reports can minimize waste generation, enhancing sustainability. |
Innovation for Sustainability |
The reporting process can inspire new sustainable practices and products, improving overall performance. |
Publicly disclosing environmental impacts creates accountability and encourages innovation. By prioritizing sustainability, you can align with global environmental goals while improving operational efficiency.
Emerging Technologies in Post-Processing
Emerging technologies are reshaping the future of post-processing. The additive manufacturing market is projected to double in size, reaching $37.2 billion by 2026. This growth is driven by advancements in materials and applications across industries like aviation, construction, and healthcare.
Evidence |
Description |
---|---|
Market Growth |
The additive manufacturing (AM) market is expected to double in size, reaching $37.2 billion by 2026. |
Industry Applications |
3D printing is being adopted across various sectors including aviation, automotive, construction, medical, and food industries. |
Material Advancements |
As technology progresses, the variety of materials used in 3D printing is increasing, leading to broader applications. |
Innovations such as AI-driven quality control and robotic surface finishing are also gaining traction. These technologies enhance precision, reduce costs, and expand the possibilities of 3D printing post-processing. By staying ahead of these trends, you can position yourself as a leader in the evolving manufacturing landscape.
Post-processing remains essential for achieving high-quality 3D-printed parts. Techniques like sanding, gap filling, and polishing enhance both functionality and aesthetics:
Benefits |
|
---|---|
Sanding |
Improves surface finish |
Gap Filling |
Enhances structural integrity |
Polishing |
Achieves a smooth aesthetic finish |
Adopting advanced automation ensures efficiency and scalability. As innovations emerge, you can unlock new possibilities, driving growth and setting higher industry standards.
FAQ
What is the most time-consuming post-processing step in 3D printing?
Support removal often takes the longest. Complex designs require precision to avoid damage, making automated solutions essential for efficiency and consistency.
How can automation improve post-processing workflows?
Automation reduces manual labor, enhances precision, and ensures consistent results. Systems like robotic surface finishing streamline operations, saving time and improving scalability for mass production.
Are post-processing techniques universal across all 3D printing technologies?
No, post-processing varies by technology. Powder-based methods need depowdering, while resin-based techniques require curing. Tailored workflows ensure optimal results for each printing method.
Leave a comment
All comments are moderated before being published.
This site is protected by hCaptcha and the hCaptcha Privacy Policy and Terms of Service apply.