FDM 3D printing stands as one of the most accessible additive manufacturing technologies available today. This process builds objects by melting thermoplastic filament and depositing it layer by layer, creating precise 3D shapes. Its simplicity and cost-effectiveness make it a preferred choice for individuals and businesses alike.
Fused deposition modeling is the most established 3D printing technology in the market.
71% of companies that use FDM/FFF technology utilize it in-house.
These statistics highlight its broad appeal and practicality. With an FDM 3D printer, users can explore endless possibilities, from prototyping to crafting customized designs.
Key Takeaways
FDM 3D printing is cheap and easy to use. It works well for both beginners and experts.
The process starts with designing a 3D model. Then, the model is sliced for printing. Finally, plastic layers are added to build the object.
You can improve prints by sanding or painting them. This makes them look better and fit for professional use.
FDM uses many materials like PLA, ABS, and PETG. These materials work for different projects and needs.
FDM is great for quick prototypes and custom designs. It helps industries like cars, planes, and schools.
How FDM 3D Printing Works
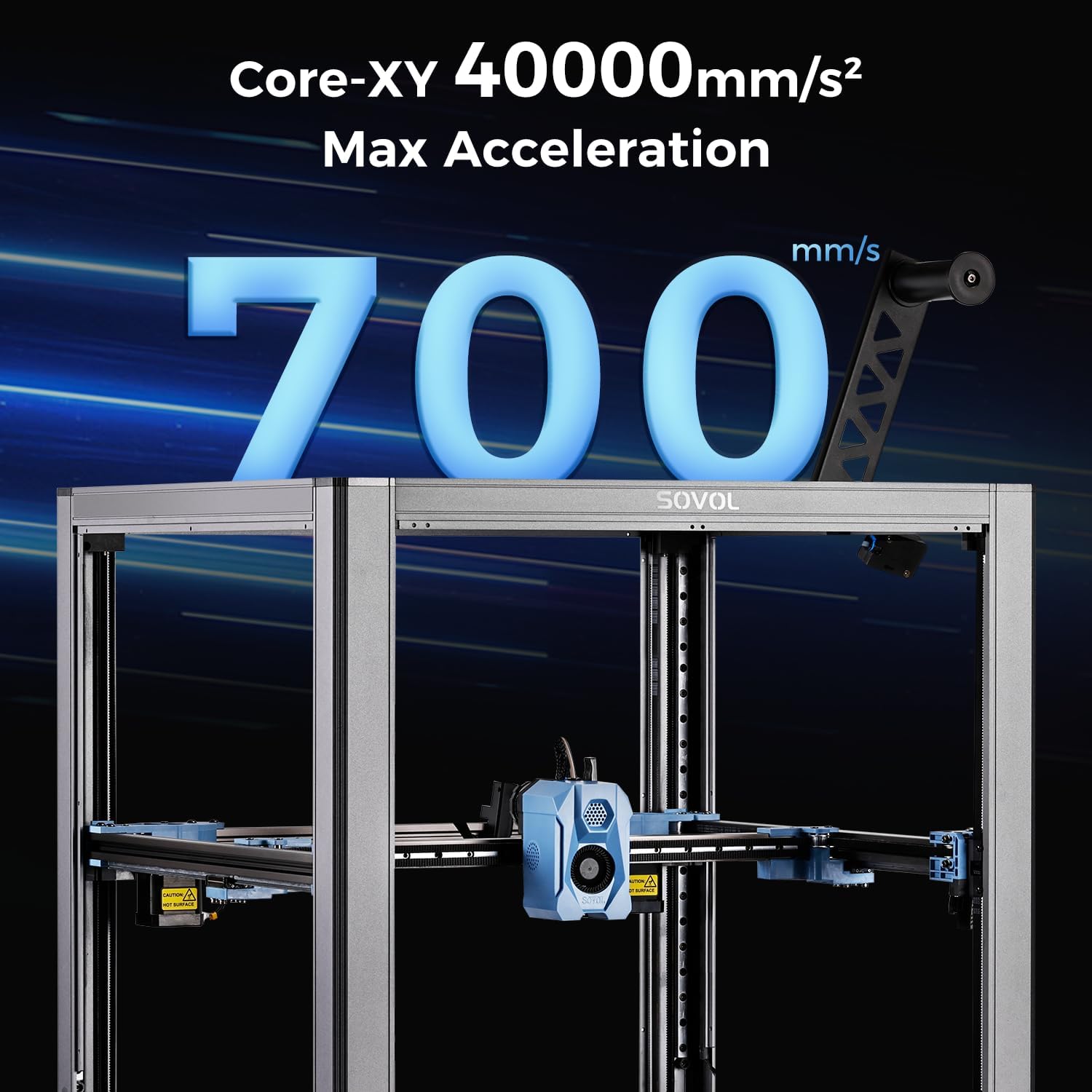
Designing the 3D Model
The process of fused deposition modeling begins with designing a 3D model. Users create these models using computer-aided design (CAD) software. This software allows them to craft intricate designs with precise dimensions. Many CAD programs offer user-friendly interfaces, making them accessible to beginners and professionals alike. Once the design is complete, it is saved in a compatible file format, such as STL or OBJ, which can be processed by slicing software.
Slicing the Model for FDM 3D Printing
Slicing transforms the 3D model into instructions that an FDM 3D printer can understand. Slicing software divides the model into horizontal layers and generates a G-code file. This file contains detailed instructions for the printer, including movement paths, extrusion rates, and layer heights. Users can adjust settings like print speed, infill density, and support structures to optimize the print. Proper slicing ensures the printer executes the design accurately, resulting in a high-quality object.
Printing the Object with an FDM 3D Printer
The actual printing process involves several steps:
FDM technology heats the filament feedstock to a semi-liquid state.
The melted material is extruded through a nozzle and deposited onto the print surface.
Each layer cools rapidly and solidifies, fusing with the previous layer.
The build platform lowers after each layer is completed, allowing the next layer to be deposited.
This layered material deposition process ensures precision and durability. Performance metrics like dimensional accuracy, surface finish, and layer adhesion highlight the reliability of FDM 3D printing.
Metric |
Description |
---|---|
Dimensional Accuracy |
Assesses if printed object dimensions match original design specifications, crucial for precise parts. |
Surface Finish |
Refers to the smoothness and visual appeal of outer layers, influenced by factors like layer height. |
Layer Adhesion and Strength |
Focuses on the bond between layers, essential for durability, influenced by temperature and material. |
FDM technology offers a dependable way to create objects with consistent quality. The Sovol SV08, for example, exemplifies this reliability with its advanced features and open-source capabilities, making it a valuable tool for both hobbyists and professionals.
Post-Processing in FDM Technology
Post-processing enhances the quality and appearance of FDM 3D-printed objects. While FDM technology produces functional parts, the layered structure often leaves visible lines and imperfections. Post-processing methods refine these prints, improving their surface finish, durability, and overall aesthetics.
Common Post-Processing Techniques
Several techniques can transform raw FDM prints into polished, professional-looking objects. Each method offers unique benefits depending on the desired outcome:
Method |
Description |
Benefits |
---|---|---|
Sanding |
A simple method using sandpaper to smooth prints. |
Reduces visibility of layer lines and imperfections. Wet sanding minimizes heat and dust. |
Painting |
Involves applying paint to hide layer lines and enhance appearance. |
Can make parts look professional and injection molded. Clear coat adds protection and shine. |
Epoxy Coating |
Applying a 2-part epoxy resin for a durable finish. |
Enhances durability and surface finish, especially when properly mixed and applied. |
Sanding is one of the most accessible methods. It involves using sandpaper of varying grits to smooth the surface. Wet sanding further reduces dust and prevents heat buildup, making it ideal for thermoplastics like PLA and ABS. Painting adds color and hides imperfections. A clear coat can also protect the surface and provide a glossy finish. For a more durable and professional result, epoxy coating creates a smooth, resilient layer that enhances both strength and appearance.
Tips for Effective Post-Processing
To achieve the best results, users should follow a few key practices. Always start with coarse sandpaper and gradually move to finer grits for a smoother finish. When painting, ensure the surface is clean and primed to improve adhesion. For epoxy coating, mix the resin thoroughly and apply it evenly to avoid bubbles or uneven textures.
Post-processing not only improves the visual appeal of FDM prints but also extends their lifespan. These techniques allow users to elevate their creations, making them suitable for professional applications or display purposes.
Materials Used in FDM 3D Printing
Common Thermoplastic Filaments (PLA, ABS, PETG)
Thermoplastic filaments dominate the materials used in FDM 3D printing due to their versatility and ease of use. PLA, ABS, and PETG are the most popular choices, each offering unique properties suited for different applications.
PLA |
ABS |
PETG |
|
---|---|---|---|
Tensile strength |
4,600 psi |
7,250 psi |
|
Elongation at break |
6% |
20% |
20-30% |
Glass transition temperature |
60-65°C |
~105°C |
85°C |
Printing temperature |
200-220°C |
220-250°C |
220-260°C |
PLA is biodegradable and easy to print, making it ideal for beginners and eco-conscious users. ABS offers superior impact resistance and flexibility, which makes it suitable for durable parts. PETG combines the strengths of PLA and ABS, providing excellent durability, tensile strength, and layer adhesion. These characteristics make PETG a versatile option for various applications.
Specialty Filaments for Advanced Applications
Specialty filaments expand the possibilities of FDM technology by offering enhanced properties. Carbon fiber-reinforced filaments provide exceptional strength and stiffness, making them ideal for aerospace and automotive industries. Flexible materials like TPU allow for the creation of elastic parts, such as gaskets and phone cases. High-temperature filaments, including polycarbonate (PC), withstand extreme conditions, making them suitable for engineering applications. These advanced materials enable users to tackle complex projects with specific performance requirements.
Choosing the Right Material for Your FDM 3D Printer
Selecting the right filament depends on several factors. Users should consider mechanical strength, temperature resistance, and printability. For example, PLA is perfect for aesthetic models, while ABS suits functional prototypes requiring durability. PETG offers a balance between strength and flexibility.
Criteria |
Description |
---|---|
Mechanical Strength |
Determines the material's ability to withstand loads. |
Temperature of Use |
Indicates how the material performs under different conditions. |
Printability |
Refers to compatibility with the printer and print quality. |
Finishing |
Evaluates the aesthetic quality and surface treatment options. |
Cost |
Helps users choose materials within their budget. |
Understanding these criteria ensures users select the best material for their specific needs, maximizing the potential of FDM 3D printing.
Advantages of FDM 3D Printing
Affordability and Accessibility
FDM technology stands out as one of the most affordable and accessible 3D printing methods available today. Its cost-effectiveness makes it an excellent choice for individuals, educators, and businesses.
FDM is recognized as the most economical method for producing custom thermoplastic parts and prototypes.
Compared to other additive manufacturing technologies, FDM 3D printers are more budget-friendly.
The wide availability of affordable thermoplastic materials further enhances its accessibility.
This affordability allows users to experiment with designs and create functional prototypes without significant financial investment. Additionally, the compact size of many FDM 3D printers makes them suitable for home, school, or office use, further increasing their accessibility.
Material Versatility in FDM Technology
FDM technology offers unmatched material versatility, enabling users to select from a wide range of thermoplastics. This flexibility supports diverse applications across industries.
Aspect |
Details |
---|---|
Technology Advancements |
Continuous improvements in FDM technology, enhancing capabilities and material compatibility. |
Material Properties |
Diverse range of thermoplastic materials available, including options for strength and biodegradability. |
Application Suitability |
Allows manufacturers to choose the most appropriate materials for their specific needs, enhancing versatility. |
The availability of materials like PLA, ABS, and PETG ensures that users can find the right option for their projects. High-performance materials, such as carbon fiber composites and engineering-grade thermoplastics, expand the possibilities for advanced applications. This versatility makes FDM 3D printing a preferred choice for industries like aerospace, automotive, and healthcare.
Ease of Use for Beginners and Professionals
FDM 3D printing is known for its simplicity, making it ideal for both beginners and experienced users. The process is straightforward, requiring minimal technical expertise to get started.
Advantage/Disadvantage |
Description |
---|---|
Ease of use |
The printing process is easy to learn and typically requires less space. |
Design flexibility |
Suitable for creating functional prototypes and models. |
Cost-effectiveness |
Low or moderate costs of equipment and post-processing. |
Beginners can quickly learn the basics of FDM technology, while professionals benefit from its reliability and precision. Features like automatic bed leveling and user-friendly slicing software simplify the workflow, ensuring consistent results. The Sovol SV08, for instance, exemplifies this ease of use with its pre-assembled design and intuitive operation, making it a valuable tool for users at any skill level.
Applications of FDM 3D Printing
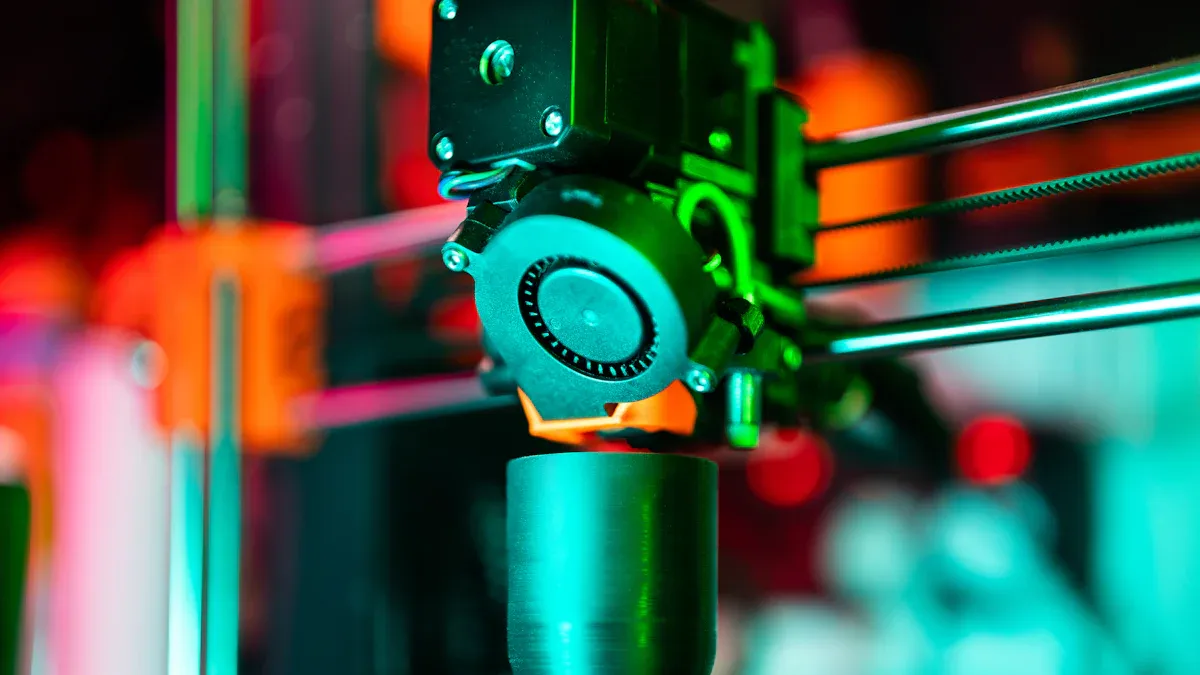
Prototyping and Product Development
FDM 3D printing plays a vital role in prototyping and product development. Its ability to create accurate models quickly and affordably makes it a preferred choice for industries like automotive, aerospace, and healthcare. Companies use FDM technology to test designs, identify flaws, and refine products before mass production.
The FDM rapid prototyping market is growing due to the increasing adoption of 3D printing across various sectors.
Industries such as healthcare benefit from customized medical devices and anatomical models.
Trends include the use of AI to optimize print parameters and the expansion of material options.
This technology also supports distributed manufacturing, enabling businesses to produce parts closer to their customers. By reducing lead times and costs, FDM 3D printers enhance the efficiency of product development processes.
Education and Learning with FDM 3D Printers
FDM 3D printers have transformed education by providing hands-on learning opportunities. Students can create physical models to better understand concepts in subjects like engineering, architecture, and math. This practical approach bridges the gap between theoretical knowledge and real-world applications.
Smart classrooms increasingly adopt 3D printing technologies to support advanced learning methods.
FDM technology is the most widely used in schools due to its user-friendly nature and affordability.
It enhances learning experiences by allowing students to visualize and interact with their designs.
Educators use FDM 3D printers to teach problem-solving and critical thinking skills. These tools prepare students for careers in technology-driven industries, fostering innovation and creativity.
Customization and Hobbyist Projects
FDM 3D printing empowers hobbyists and makers to bring their ideas to life. Its versatility and affordability make it an excellent choice for creating customized items. Users can design and print unique objects, from decorative pieces to functional tools.
Aspect |
Description |
---|---|
Prototyping |
FDM enables rapid iteration of designs, allowing users to refine their creations efficiently. |
Material Versatility |
A wide range of thermoplastic materials supports diverse applications, from flexible to durable parts. |
Cost-Effectiveness |
FDM remains one of the most affordable 3D printing methods, making it accessible to hobbyists. |
Hobbyists often experiment with materials like PLA, ABS, and carbon fiber-infused filaments to achieve specific properties. This flexibility allows them to tackle various projects, from artistic creations to engineering prototypes. FDM technology continues to inspire creativity and innovation in the maker community.
Industrial and Commercial Applications
FDM 3D printing has revolutionized industrial and commercial manufacturing by offering a cost-effective and efficient solution for producing high-quality parts. Its ability to create durable and dimensionally accurate components has made it a preferred choice across various industries.
Key Industries Leveraging FDM Technology
Automotive: Manufacturers use FDM 3D printing to create prototypes, jigs, and fixtures. This technology accelerates the design process and reduces production costs.
Aerospace: Lightweight and strong parts, such as brackets and housings, are produced using advanced thermoplastics like carbon fiber-reinforced filaments.
Healthcare: FDM printers create custom medical devices, prosthetics, and anatomical models, improving patient care and reducing lead times.
Consumer Goods: Companies rely on FDM technology to produce small-batch products, customized items, and packaging prototypes.
Benefits for Industrial and Commercial Use
FDM technology captured the largest market share in 2024, highlighting its widespread adoption. Businesses value its ability to produce durable and dimensionally stable products. Approximately 71% of companies utilize FDM printers for manufacturing functional parts and tools. This widespread use demonstrates the reliability and versatility of the technology.
Feature |
Industrial Advantage |
---|---|
Rapid Prototyping |
Speeds up product development cycles, enabling faster time-to-market. |
Material Versatility |
Supports engineering-grade thermoplastics for demanding applications. |
Cost Efficiency |
Reduces tooling costs and material waste compared to traditional manufacturing methods. |
Real-World Impact
FDM 3D printing enables manufacturers to adopt on-demand production models. This approach minimizes inventory costs and shortens supply chains. For example, automotive companies can print replacement parts locally, reducing shipping delays. Similarly, healthcare providers can create patient-specific devices, ensuring a perfect fit and improved functionality.
The Sovol SV08 exemplifies the potential of FDM technology in industrial applications. Its large build volume and compatibility with advanced materials make it ideal for producing robust, high-performance parts. By integrating FDM 3D printing into their workflows, businesses can achieve greater efficiency and innovation.
Best Practices for FDM 3D Printing
Preparing Your FDM 3D Printer and Workspace
Proper preparation ensures consistent results and extends the lifespan of an FDM 3D printer. A well-organized workspace minimizes errors and enhances safety. Follow these steps to prepare effectively:
Inspect the Printer: Regularly check for loose components, worn belts, or clogged nozzles. Preventive maintenance avoids unexpected failures.
Calibrate the Printer: Ensure the bed is level and the nozzle height is accurate. Automatic bed leveling features, like those in the Sovol SV08, simplify this process.
Organize the Workspace: Keep tools, filaments, and cleaning supplies within reach. A clean, dust-free environment improves print quality.
Resources like "3D Printing The Ultimate Guide" and "Maintaining and Troubleshooting Your 3D Printer" provide detailed insights into setup and maintenance, making them valuable references for users.
Optimizing Print Settings for Fused Deposition Modeling
Fine-tuning print settings enhances the performance of FDM technology. Adjustments to parameters like speed, temperature, and layer height can significantly impact the final output.
Metric |
Trial I (MPa) |
Trial III (MPa) |
Trial C (MPa) |
---|---|---|---|
52.3 - 63.4 |
50.4 - 69.1 |
N/A |
|
Young’s Modulus |
N/A |
735.6 |
N/A |
Ultimate Flexural Strength |
72 - 89 |
N/A |
N/A |
Ultimate Compressive Strength |
N/A |
N/A |
85.3 |
This table highlights how optimized settings improve mechanical properties. For example, adjusting the nozzle temperature can enhance layer adhesion, while reducing print speed improves surface finish. Experimenting with slicer settings allows users to achieve the desired balance between quality and efficiency.
Troubleshooting Common Issues in FDM Technology
Despite its reliability, FDM technology may encounter challenges. Identifying and resolving these issues ensures uninterrupted printing.
Layer Shifting: Check for loose belts or misaligned components. Tightening belts and recalibrating the printer often resolves this problem.
Poor Adhesion: Ensure the print bed is clean and properly leveled. Using adhesives like glue sticks or specialized sprays can improve adhesion.
Stringing or Oozing: Adjust retraction settings and nozzle temperature to minimize filament leakage.
FDM systems, like those used in aviation, demonstrate how monitoring and analyzing data can prevent recurring issues. By applying similar principles, users can proactively address problems and maintain optimal printer performance.
Maintaining Your Sovol SV08 for Long-Term Performance
Proper maintenance of the Sovol SV08 ensures consistent performance and extends its lifespan. Regular care also minimizes downtime and prevents costly repairs. Follow these essential tips to keep your printer in excellent condition.
1. Clean the Printer Regularly
Dust and filament residue can accumulate on the Sovol SV08, affecting its performance. Use a soft brush or compressed air to clean the nozzle, build plate, and extruder. Avoid using water or harsh chemicals, as they may damage sensitive components.
Tip: Clean the nozzle after every print to prevent clogs and ensure smooth extrusion.
2. Lubricate Moving Parts
The Sovol SV08 relies on smooth motion for precise printing. Apply a small amount of lubricant to the linear rails, lead screws, and bearings. Use a high-quality lubricant designed for 3D printers to reduce friction and wear.
3. Inspect and Tighten Components
Loose screws or belts can cause print defects. Regularly inspect the frame, belts, and pulleys for signs of wear or looseness. Tighten any loose parts to maintain stability and accuracy.
Component |
Maintenance Frequency |
Action |
---|---|---|
Nozzle |
After every print |
Clean to remove filament residue. |
Belts and Pulleys |
Weekly |
Check tension and tighten if needed. |
Linear Rails |
Monthly |
Lubricate to ensure smooth motion. |
4. Update Firmware and Software
Sovol provides open-source firmware for the SV08, allowing users to access the latest features and improvements. Visit the Sovol Wiki to download updates and follow installation instructions.
5. Store Filaments Properly
Moisture can degrade filament quality, leading to poor prints. Store filaments in a dry, airtight container or use a filament dryer like the Sovol SH01.
Note: Proper filament storage ensures consistent print quality and reduces material waste.
By following these maintenance practices, users can maximize the performance and durability of their Sovol SV08. Regular care not only enhances print quality but also ensures a reliable and enjoyable 3D printing experience.
FDM 3D printing offers a straightforward process that builds objects layer by layer with precision and reliability. Its ability to produce both prototypes and final products highlights its versatility across industries. Dimensional accuracy and repeatability make it a trusted choice for applications requiring high standards. Users value its accessibility, as it supports a wide range of materials and fits various budgets.
The Sovol SV08 exemplifies the potential of FDM technology. Its advanced features and open-source design empower users to create with confidence. Exploring solutions like the SV08 unlocks endless possibilities for innovation and creativity.
FAQ
What is the difference between FDM and fused filament fabrication?
FDM and fused filament fabrication refer to the same additive manufacturing technology. FDM is a trademarked term, while fused filament fabrication is the generic name. Both describe the process of depositing melted thermoplastic filament layer by layer to create 3D objects.
How durable are FDM printed parts?
FDM printed parts are durable and suitable for functional applications. Their strength depends on the material used, print settings, and layer adhesion. Materials like ABS and PETG offer higher durability, while PLA is more brittle but easier to print.
Can the FDM process handle flexible materials?
Yes, the FDM process supports flexible materials like TPU. These materials allow users to create elastic parts such as gaskets and phone cases. However, printing flexible filaments requires precise settings and a compatible extruder, like the dual-gear direct drive extruder in the Sovol SV08.
What industries benefit from FDM technology?
Industries like automotive, aerospace, healthcare, and education benefit from FDM technology. It enables rapid prototyping, custom part production, and hands-on learning. Its affordability and material versatility make it a valuable tool for various applications.
How does FDM compare to other additive manufacturing technologies?
FDM is more affordable and accessible than many other additive manufacturing technologies. It excels in creating prototypes and functional parts with thermoplastics. While it may lack the precision of resin-based methods, its simplicity and material options make it a popular choice.
Leave a comment
All comments are moderated before being published.
This site is protected by hCaptcha and the hCaptcha Privacy Policy and Terms of Service apply.