Turbine scanning captures precise 3D data of turbine components, ensuring manufacturing accuracy. You can verify critical features like hole placement and surface roughness using high-resolution scans. Advanced scanning methods reduce inspection time from hours to minutes. Additionally, researchers have developed enhanced 3D printing techniques to minimize cracking and improve turbine blade performance.
Key Takeaways
- Turbine scanning collects exact 3D details for making and checking parts.
- Using turbine scanning with 3D printing saves money and time. It helps make good parts quickly.
- Accurate scans help redesign and improve parts, making turbines work better.
Understanding Turbine Scanning Technology
What is Turbine Scanning?
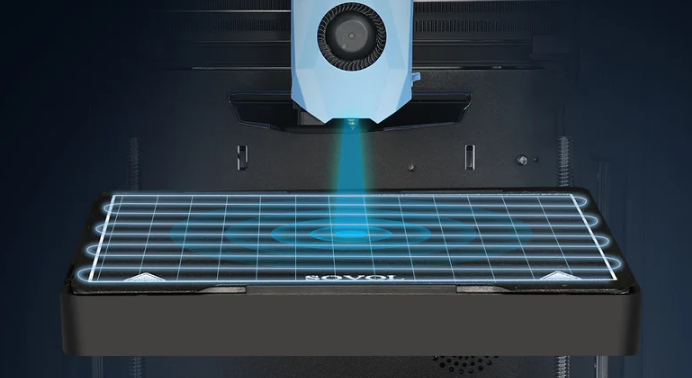
Turbine scanning is a cutting-edge process that captures detailed 3D data of turbine components. This technology ensures that every aspect of a turbine, from its blades to its rotor, is accurately measured and analyzed. By using advanced 3D scanning systems, you can create precise digital models that replicate the physical structure of turbomachinery. These models are essential for applications like reverse engineering, quality control, and performance optimization.
The importance of turbine scanning lies in its ability to handle the complex geometries of turbomachinery. For example, turbine blades often feature intricate curves and edges that require high-resolution scans to capture their exact shape. This level of detail ensures that the scanned data can be used for accurate manufacturing and inspection processes. Additionally, turbine scanning plays a critical role in turbomachinery manufacturing by enabling engineers to meet strict industry standards, such as those set by the FAA for aerospace components.
Source |
Description |
---|---|
Measuring Impeller Turbines in Harsh Manufacturing Environments |
Highlights the need for precise measurement techniques in hydropower plants to assess turbine conditions and loads. |
Dimensional Inspection of Turbine Blades Using 3D Scanning |
Describes how blue light scanners collect millions of data points to create detailed 3D models of turbine blades. |
Turbine Blades Reverse Engineered to Strict FAA Standards with 3D Laser Scanning |
Emphasizes the importance of quality and safety in turbine blade manufacturing under FAA standards. |
Metrology within the Aerospace, Airfoil, IGT, and Power Generation Industries |
Explains how accurate scan data improves performance analysis through Computational Fluid Dynamics and Finite Element Analysis. |
Key Methods in Scanning: Laser Scanning and 3D Measurement of Water Turbines
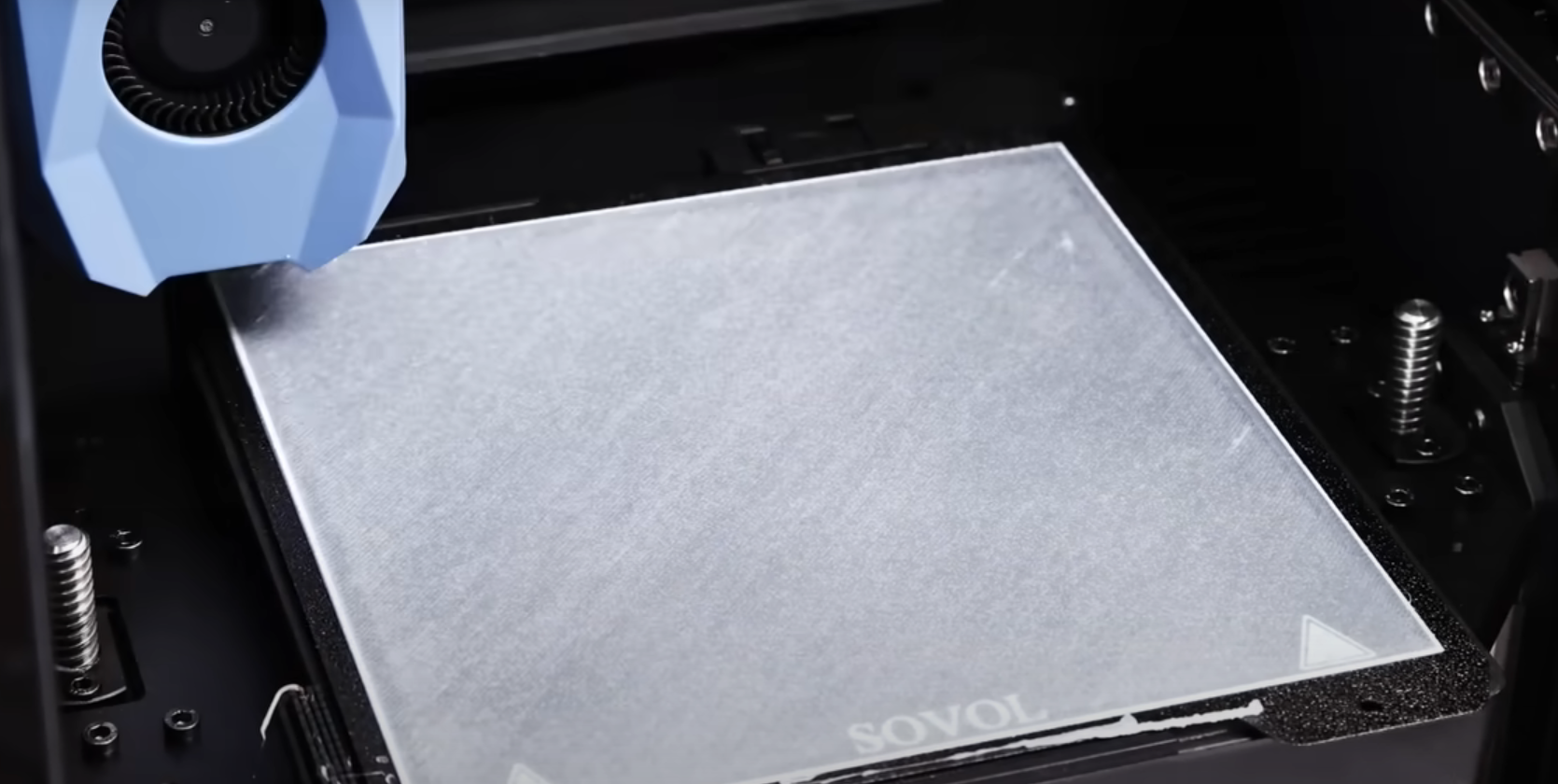
Two primary methods dominate turbine scanning: laser scanning and 3D measurement of water turbines. Laser scanning uses focused laser beams to capture millions of data points from a turbine's surface. This method is highly effective for creating full 3D rotor scans, which are essential for analyzing the performance and efficiency of turbomachinery. Laser scanning also excels in detecting minor deviations in turbine blades, ensuring that manufacturing processes meet the highest standards of accuracy.
The 3D measurement of water turbines, on the other hand, is particularly useful in hydroelectric power plants. This method allows you to evaluate the condition and efficiency of water turbines by generating precise digital models. These models can identify slight deviations from ideal rotor geometry, enabling engineers to make necessary adjustments. Additionally, the scanned data can be compared with existing CAD models or mirrored for symmetry checks, ensuring that the turbine operates at peak performance.
- 3D scanning has been successfully implemented in hydroelectric power plants to assess turbine conditions and efficiency.
- The technology enables the creation of precise digital models for manufacturing new components.
- High-accuracy measurements detect even minor deviations in large and complex turbine components.
Importance of Precision in Capturing Complex Geometries
Precision is the cornerstone of turbine scanning. Turbomachinery components, such as rotors and blades, feature intricate designs that demand meticulous attention to detail. A full 3D rotor scan, for instance, captures every curve and edge of the rotor, ensuring that no detail is overlooked. This level of precision is crucial for applications like reverse engineering, where accurate data is needed to recreate or optimize existing designs.
Accurate scanning also enhances the inspection process by identifying irregularities that might compromise the performance of turbomachinery. For example, a detailed 3D model can reveal significant irregularities in blade installation or deviations from the ideal rotor geometry. By addressing these issues early, you can improve the efficiency and reliability of the turbine.
Moreover, precise scan data supports advanced engineering analyses, such as Computational Fluid Dynamics (CFD) and Finite Element Analysis (FEA). These analyses help engineers optimize the design and performance of turbomachinery, ensuring that it meets the demands of modern industries.
Applications of Turbine Scanning in 3D Printing
Creating Accurate Turbine 3D Models for Manufacturing
Turbine scanning plays a pivotal role in creating precise turbine 3D models for manufacturing. By capturing intricate details of turbine blades and rotors, you can generate accurate digital replicas that serve as the foundation for production. These models ensure that every component meets strict design tolerances, reducing the risk of defects during manufacturing.
The enhanced scanning process provides complete data sets, capturing geometric details like sharp edges and complex curves. This precision allows you to perform reliable reverse engineering and conduct thorough quality assessments. For instance:
- High-tech 3D scanning systems enable detailed measurements of turbine parts, ensuring that even the smallest deviations are identified.
- Manufacturers can compare scanned data against design specifications to detect defects in real time.
- This process ensures that only components meeting quality standards proceed to the next stage of production.
The integration of 3D scanning technology has revolutionized inspection processes. It addresses long-standing challenges in turbomachinery manufacturing and enhances overall efficiency. By leveraging these precise digital copies, you can streamline production workflows and maintain consistency across all turbine components.
Reverse Engineering and Design Optimization
Reverse engineering, powered by turbine scanning, allows you to recreate and optimize existing turbine components. This process is particularly valuable for maintaining legacy systems or improving the performance of current designs. By scanning turbine blades and rotors, you can generate precise digital copies that serve as a baseline for new designs or replacement parts.
A case study on Solar Turbines highlights the impact of 3D scanning in reverse engineering. From 2006 to 2014, the company used ATOS 3D scanning technology to enhance the accuracy and efficiency of turbine component design. This approach not only improved safety and performance but also streamlined the development of replacement parts.
Additional examples demonstrate the benefits of reverse engineering:
- Scanning a turbine blade to create a 3D digital file enabled the production of an exact match, saving 10,000 man-hours over the project's lifespan.
- By documenting actual components through scanning, you can ensure compatibility with existing assemblies, which is crucial for transitioning to new technologies like electric vehicles.
This process also facilitates design optimization. With detailed scan data, you can identify areas for improvement, such as enhancing aerodynamics or reducing material waste. These optimizations lead to more efficient and reliable turbomachinery.
3D Printing for Turbine Parts: Enhancing Efficiency and Quality
The combination of turbine scanning and 3D printing has transformed the production of turbine parts. By using accurate 3D models generated from scans, you can produce high-quality components with reduced lead times and costs. This approach is particularly effective for manufacturing turbine blades and other complex parts.
Performance metrics highlight the advantages of this integration:
Improvement Type |
Statistic |
---|---|
Development Time |
Reduced from two years to just two months |
Repair Time |
Reduced by 90% |
Production Time for Impeller |
Approximately 48 hours compared to casting |
These improvements demonstrate how 3D printing for turbine parts enhances efficiency and quality. For example, 3D-printed parts can be produced faster than traditional methods, allowing you to respond quickly to market demands. Additionally, the precision of 3D printing ensures that each component meets stringent performance requirements.
By combining turbine scanning with advanced 3D printing techniques, you can achieve unparalleled accuracy and reliability in turbomachinery manufacturing. This synergy not only improves production processes but also paves the way for innovation in turbine design and performance.
Benefits of Integrating Turbine Scanning with 3D Printing
Cost Reduction and Faster Prototyping
Integrating turbine scanning with 3D printing significantly reduces costs and accelerates prototyping. Traditional manufacturing methods often result in material waste, especially when working with high-value metals. In contrast, 3D printing employs an additive approach, constructing components layer by layer and using only the required materials. This process minimizes waste and lowers operational expenses. For complex turbomachinery designs, this efficiency is particularly advantageous.
Additionally, 3D printing streamlines the prototyping process. By transitioning directly from CAD designs to production, you can create and test prototypes within days or weeks. This rapid cycle reduces labor costs and shortens development timelines. Industries like renewable energy have already adopted this technology to produce intricate geometries with high precision, showcasing its ability to enhance both speed and cost-effectiveness.
Improved Design Flexibility and Customization
The combination of turbine scanning and 3D printing offers unparalleled design flexibility. Scanning captures the precise geometry of components like rotors and blades, enabling you to create highly detailed digital models. These models serve as a foundation for customizing designs to meet specific performance requirements.
For example, you can optimize internal flow paths in turbine components to improve fuel atomization or enhance aerodynamics. This level of customization is challenging to achieve with traditional manufacturing methods. Furthermore, the ability to modify designs quickly allows you to adapt to changing industry demands, ensuring that your turbomachinery remains competitive and efficient.
Enhanced Performance of Turbine Components
Integrating scanning and 3D printing techniques improves the performance of turbine components. Precise scans ensure that every detail of a rotor or blade is captured, enabling the production of high-quality parts. Advanced manufacturing metrics highlight these benefits:
Metric |
Evidence |
---|---|
Lead Time Reduction |
Designs can go from CAD to printer, allowing rapid prototyping and testing within days or weeks. |
Weight Reduction |
GE’s LEAP nozzle achieved a 25% weight reduction through AM and design optimization. |
Enhanced Performance |
Optimized internal flow paths improve fuel atomization, boosting combustion efficiency. |
Durability |
Monolithic parts enhance structural integrity and fatigue life under high-pressure conditions. |
These improvements translate to better durability, efficiency, and reliability in turbomachinery. By leveraging scanning and 3D printing, you can produce components that meet the highest performance standards while reducing production time and costs.
Turbine scanning has revolutionized 3D printing by improving manufacturing precision and efficiency. By capturing intricate geometries, you can ensure turbine components meet strict quality standards. Combining these technologies reduces costs, accelerates prototyping, and enhances design flexibility.
Future advancements promise even greater possibilities:
- Material Diversity: New composites and alloys expand 3D printing applications.
- AI Integration: Machine learning improves scanning accuracy and efficiency.
- Large-Scale Manufacturing: Industries like aerospace benefit from streamlined production of complex turbine parts.
These innovations will continue driving cost savings, customization, and performance improvements in turbine production.
FAQ
What is turbine scanning, and why is it important for 3D printing?
Turbine scanning captures precise 3D data of components. It ensures manufacturing accuracy, improves design optimization, and enhances the quality of printed turbine parts.
How does turbine scanning improve reverse engineering?
Scanning creates detailed digital models of turbine components. These models help you recreate, optimize, and manufacture parts with high precision and efficiency.
Can turbine scanning reduce production costs?
Yes, turbine scanning minimizes material waste and accelerates prototyping. This reduces operational expenses and shortens development timelines for turbomachinery manufacturing.
Lascia un commento
Tutti i commenti sono moderati prima di essere pubblicati.
Questo sito è protetto da hCaptcha e applica le Norme sulla privacy e i Termini di servizio di hCaptcha.